Your cart is currently empty!
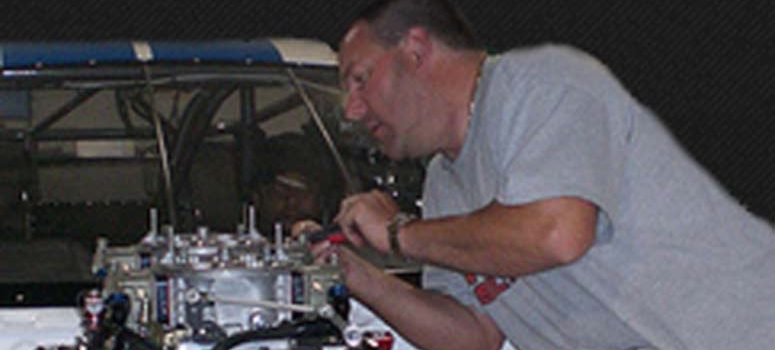
Just My Two Cents on Flowing Your Fuel Pressure
Help with: Flowing Fuel Pressure Jets
Many have asked about flowing fuel pressure jets. Asking what jet to flow their system with? “Do I use a 70 “Holley” or a .073 “nitrous” jet?” Actually, these are the same. Nitrous jets are numbered in thousandths on an inch. Holley jets are numbered by drill size.
Most have heard that with a direct port system you should use the square area method. Take the jet size squared times the number of jets. Then take the square root of this number.
For example…
A system with eight .032 fuel jets is 32 X 32 = 1024. Then you take 1024 X 8 (jets) =8192. The square root of 8192 is 90.509, thus telling you that for the eight .032 fuel jets it wants you to flow thru a .090 jet.
Needless to say, the larger the fuel jets you’re using, the larger your flow jet gets! The larger your flow jet gets, the lower your regulator would read. Fix this by adjusting the regulator back up in pressure, for the larger, more free flowing jet.
With each set of larger fuel jets you use, it’s going to tell you to raise the fuel pressure each time! This is an important bit of info when flowing fuel pressure jets.
A few things this method does not take into consideration, when flowing fuel pressure jets, would be;
- Let’s try and use round numbers for the ease of this.. Let’s look at the average direct port system it has two nitrous solenoids with say .115 orifices in them. Then you have to fuel solenoids with .156 orifices in each of them. So that being said you can see that the nitrous solenoid starts out being smaller then the fuel side by over .040.
- Then let’s take a look at the pressure the systems each run at. Again, for sake of round numbers we’ll say that you are using 1000 PSI on your nitrous pressure and 10 PSI on the fuel pressure. That being said, the nitrous is running at 100 times the fuel pressure!
- Then let’s take the last piece of the puzzle and look at it. As far as nitrous to fuel ratio’s go many of you have heard us talking about running a N/F ratio of let’s say 6 to 1. Meaning you need 6 parts nitrous, to every one part of fuel..
Can you see where this is going? You have fuel solenoids on each side of your engine that are already .041 larger then you nitrous solenoids, you are trying to force the nitrous through the system at roughly 100 times the pressure of the fuel side. Last but not least, you need 6+ times more nitrous than fuel to have a proper nitrous to fuel ratio! By design how is the nitrous ever to keep up with the fuel gains?
If you have a four jet spread (larger nitrous then fuel ) and a 5.5 PSI in fuel pressure and you start with a .024 nitrous and a .020 fuel jet as you work you way up to a .032 nitrous and a .028 fuel jet, the system gets richer with each larger jet change – just because your inching your way closer to the max area of the nitrous solenoids.
Think about this, how many times have you read where a guy say this solenoid won’t flow more than a .038 jet or a .042? Ever think that the solenoid isn’t the problem? Maybe the tune up or tuner is the issue? If you take your average .115 orifice nitrous solenoid ( area of .010386) and divide it into 4 jets it will mathematically flow at least 4 .057 (.002551) jets. But again, this doesn’t take into consideration the pressure drop across the solenoid either.
If you have an out-of-the-box plate system, in most cases, you may be better off to flow through the fuel jet your going to use in the spray bar. This is how most manufactures have chosen to set up their systems. That being said, when we flow a plate system and re map them we do this using a .073 orifice to flow through on all settings. Some do, some don’t!
If you’ve made it this far, I thank you for your time. Just my two cents on flowing fuel jets.
Thanks,
Steve Johnson
Induction Solutions